
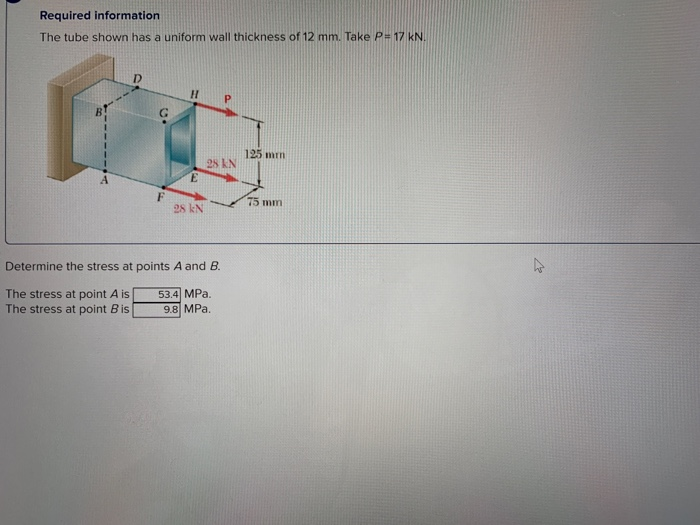
There are three main approaches to manufacturing tubular structures, including inkjet printing, laser-assisted drop on demand printing, and extrusion-based methods, which include filament assembly method and using a coaxial needle. Since drug delivery behavior can be characterized by the outer gel layer in gel-formed matrices in drug delivery, hydrogel tubular structures printed by coaxial needles can be utilized as a matrix or encapsulate powder compounds or other drugs. Hydrogel materials that can be fabricated layer by layer have been used to create a vehicle for drug delivery. 3D printing is considered to be a transformative technology for creating personalized drug delivery systems. Another application for 3D printed tubular structures is in drug delivery. Without a proper vascular system, the printed cells will not survive, and many researchers have tried to solve this problem. The vascular system is critical for supplying oxygen, growth factors, and nutrients to the cell and removes waste products for large-scale cell growth or organ printing.
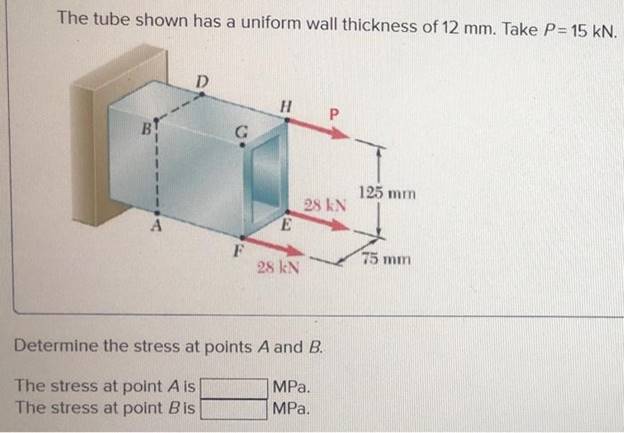
One main application of the 3D printed tubular structure is used to mimick or grow a vascular system for use in tissue engineering. In addition to the fabrication of scaffolds and porous structures, 3D printing of tubular structures has drawn increased attention. Changing the inner needle size or the flow velocity both affect the heat exchange and thus the temperature-dependent dynamic viscosity. The dynamic viscosity of GG determines the pressure equilibrium and the range of achievable wall thickness. A finite element model was developed to estimate the temperature distribution and the wall thickness. Encapsulation is possible in a smaller range of flow velocities in both needle combinations. Two pairs of coaxial needles were used which are 18-12 gauge (G) and 20-12G. The wall thickness is controlled by changing the relative flow velocity of the inner needle (phosphate-buffered saline, PBS) to the outer needle, while keeping the velocity of outer needles (GG) constant. The objectives of this study are to investigate the thermal extrusion process of GG to form tubular structures, the range of achievable wall thickness, and a possibility to form tubular structures with closed ends to encapsulate fluid or drug inside the tube. In this study, we used the coaxial extrusion process to fabricate tubular structures with varying wall thicknesses using a thermal-crosslinking hydrogel, gellan gum (GG). The wall thickness of the tube determines the delivery rate. Tubular structures of the hydrogel are used in a variety of applications such as delivering nutrient supplies for 3D cell culturing. Journal of Verification, Validation and Uncertainty Quantification.Journal of Thermal Science and Engineering Applications.Journal of Offshore Mechanics and Arctic Engineering.Journal of Nuclear Engineering and Radiation Science.Journal of Nondestructive Evaluation, Diagnostics and Prognostics of Engineering Systems.Journal of Nanotechnology in Engineering and Medicine.Journal of Micro and Nano-Manufacturing.Journal of Manufacturing Science and Engineering.Journal of Engineering Materials and Technology.Journal of Engineering for Sustainable Buildings and Cities.Journal of Engineering for Gas Turbines and Power.Journal of Engineering and Science in Medical Diagnostics and Therapy.Journal of Electrochemical Energy Conversion and Storage.Journal of Dynamic Systems, Measurement, and Control.Journal of Computing and Information Science in Engineering.Journal of Computational and Nonlinear Dynamics.Journal of Autonomous Vehicles and Systems.ASME Letters in Dynamic Systems and Control.ASCE-ASME Journal of Risk and Uncertainty in Engineering Systems, Part B: Mechanical Engineering.

Mechanical Engineering Magazine Select Articles.
